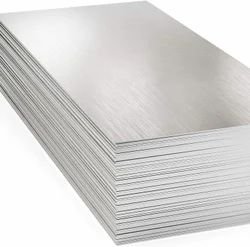
Inconel 601 is an alloy widely praised for its excellent oxidation and high-temperature corrosion resistance. With its high content of nickel and chromium, this alloy is particularly valued in industries where durability under extreme temperatures is essential. To maximize the performance and longevity of Inconel 601, proper annealing is crucial. Annealing improves the material’s durability, mechanical properties, and workability, making it easier to machine and form while enhancing its corrosion resistance. In this article, we’ll explore effective annealing techniques for Inconel 601 and discuss how inconel suppliers can ensure their products meet demanding application requirements.
Understanding Inconel 601: Composition and Properties
Inconel 601 is a nickel-chromium alloy containing approximately 60% nickel, 23% chromium, and a small amount of aluminum, which helps form a protective oxide layer. This composition gives Inconel 601 its unique properties, including:
– Exceptional Oxidation Resistance: Inconel 601 can withstand high temperatures without oxidizing, even in conditions where other metals would deteriorate.
– High Durability: The alloy’s composition makes it robust and resistant to corrosion, which is essential for applications in industries like aerospace, power generation, and petrochemicals.
– Stability at High Temperatures: Inconel 601 maintains its strength and stability up to 2200°F (1204°C), making it suitable for high-stress environments.
Annealing helps further optimize these properties by reducing internal stresses, improving ductility, and enhancing machinability, which are beneficial for both the manufacturer and the end-user.
What is Annealing, and Why is it Important for Inconel 601?
Annealing is a heat treatment process that alters the microstructure of the alloy, making it softer and more pliable. This process involves heating the material to a specific temperature, holding it there for a designated time, and then cooling it down at a controlled rate. For Inconel 601, annealing allows for:
1. Enhanced Workability: Annealed Inconel 601 becomes easier to shape, cut, and form without the risk of cracks or fractures.
2. Improved Corrosion Resistance: Proper annealing enhances the alloy’s resistance to oxidation and corrosion, vital for high-stress applications.
3. Reduced Stress and Increased Durability: Annealing reduces internal stresses, making Inconel 601 less prone to mechanical failure over time.
Inconel suppliers typically recommend annealing as part of the manufacturing process to maximize Inconel 601’s lifespan and performance.
Key Steps to Effectively Anneal Inconel 601
1. Preparation and Cleanliness
Before annealing, Inconel 601 should be thoroughly cleaned to remove any contaminants, oils, or residues. These impurities can affect the quality of the heat treatment process and compromise the alloy’s properties. Inconel suppliers often emphasize the importance of cleanliness, as surface contaminants can hinder the formation of the protective oxide layer.
2. Selecting the Proper Furnace Atmosphere
For Inconel 601, a controlled atmosphere is essential to prevent unwanted reactions. Annealing should take place in a vacuum or an inert atmosphere, such as argon, to protect the metal surface from oxidation or contamination. This step ensures the integrity of the Inconel 601 alloy and helps maintain its corrosion resistance.
3. Heating to the Annealing Temperature
Inconel 601’s annealing process typically requires heating the alloy to a temperature range of 1870°F to 2150°F (1020°C to 1177°C). This temperature range allows the alloy to become soft and malleable without losing its key mechanical properties. Holding time varies based on the thickness of the material; inconel suppliers generally recommend holding the alloy at the annealing temperature for approximately 1 to 2 hours per inch of thickness.
4. Controlled Cooling Process
After reaching the desired annealing temperature, Inconel 601 should be cooled down at a controlled rate. Rapid quenching is usually avoided, as it can introduce stresses or cause the formation of unwanted microstructures. Instead, Inconel 601 is often allowed to cool slowly in the furnace or air-cooled, depending on the specific application requirements. Tool steel suppliers emphasize that the cooling process should be carefully managed to ensure a uniform and consistent result.
Avoiding Common Annealing Mistakes with Inconel 601
Even minor variations in the annealing process can affect the durability and performance of Inconel 601. Here are some common mistakes to avoid:
– Incorrect Temperature Control: Overheating or underheating can result in incomplete annealing, reducing the alloy’s durability and workability.
– Inadequate Furnace Atmosphere: Oxygen exposure during annealing can lead to oxidation, compromising the protective oxide layer that gives Inconel 601 its corrosion resistance.
– Improper Cooling Rate: Rapid cooling can create internal stresses, leading to decreased durability. Inconel suppliers advise careful attention to the cooling rate to prevent cracks or structural changes.
Quality Assurance from Inconel Suppliers
To ensure that Inconel 601 meets the highest standards, inconel suppliers implement strict quality assurance procedures during the annealing process. These procedures may include:
1. Temperature Monitoring and Control: Inconel suppliers use advanced temperature control systems to ensure precise heating and cooling, optimizing the alloy’s durability and workability.
2. Microstructural Analysis: After annealing, inconel suppliers often conduct microscopic analysis to verify the alloy’s grain structure and detect any potential flaws.
3. Mechanical Testing: Tensile strength, hardness, and impact tests are conducted to confirm the desired properties, ensuring that Inconel 601 can withstand high-stress environments.
Applications of Annealed Inconel 601
Inconel 601’s durability after proper annealing makes it highly versatile in various industries. Its applications include:
– Aerospace Components: High-temperature aerospace components, such as exhaust systems and combustion liners, rely on annealed Inconel 601 for strength and oxidation resistance.
– Thermocouple Protection Tubes: Used in extreme environments, annealed Inconel 601 provides longevity and stability, making it a preferred choice for thermocouple protection tubes.
– Industrial Furnace Components: Inconel 601’s high-temperature performance and oxidation resistance make it ideal for furnace components, where durability is crucial.
Inconel suppliers ensure that annealed Inconel 601 meets the rigorous demands of these industries, contributing to the alloy’s reputation as a reliable and robust material for extreme applications.
The Role of Annealing in Inconel 601’s Lifespan
Annealing plays an integral role in enhancing Inconel 601’s resilience, extending its usable lifespan in applications where mechanical strength and oxidation resistance are essential. Without proper annealing, Inconel 601 may be more susceptible to mechanical stress and reduced performance, particularly in high-temperature environments.
How to Choose the Right Inconel Suppliers
Selecting reputable inconel suppliers is critical to ensure the quality and durability of Inconel 601. Suppliers should offer:
– Certified Material: Inconel suppliers should provide certification and testing data to confirm the alloy meets industry standards.
– Quality Control Protocols: Look for suppliers who use advanced quality assurance procedures, including testing for mechanical and corrosion resistance properties.
– Technical Expertise: Inconel suppliers with a thorough understanding of annealing and heat treatment processes can provide guidance and support to optimize material performance.
Conclusion
Proper annealing of Inconel 601 is essential to maximize its durability, workability, and corrosion resistance. By following precise heating, holding, and cooling procedures, Inconel suppliers ensure the material’s performance in demanding applications. Whether for aerospace, industrial furnaces, or chemical processing equipment, annealed Inconel 601 offers the durability needed to withstand extreme environments. As industries continue to require materials that deliver under stress, Inconel 601’s resilience, supported by expert annealing from trusted inconel suppliers, will remain a vital resource for high-performance applications.